The Yamatomichi Muffler will be exhibited and sold for a limited time at the company’s directly managed stores as a part of the “zero waste” project.
Introduction
Scarf Made from Surplus Materials
During the production of the 100% Merino series in 2022, although initially approving the mass production of the fabric used for cuffs and ribs, we decided to shelve it with a heavy heart and start anew. Thanks to this decision, we were able to create a product that we were truly satisfied with. However, we were left with a lot of unused materials.
Although the fabric was not sufficient for use in cuffs and ribs, being made of 100% Merino wool, I couldn’t bear to throw it away and wanted to somehow use it. So, with the help of graphic designer Hideyuki Yamano, we created blankets.
However, in the process of making the blanket, a small amount of leftover fabric was created. Determined not to waste it, we were able to create this incredibly soft and comfortable scarf.
Design

Hideyuki Yamano
Graphic designer. Born in Nara. In 2009, he established the design firm TAKAIYAMA inc. He engages in graphic design activities ranging from advertising, books, architectural signage to brand design, covering both two-dimensional and spatial design. Additionally, he holds exhibitions and creates works under his own name. He has presented works such as “Kusobadge,” “B.C.G,” “YAMANOMAX,” and “UHS-α.”
http://takaiyama.jp/
Production Story
Zero Waste Design
Hideyuki Yamano of TAKAIYAMA inc. was the designer behind the Yamatomichi Blanket and Yamatomichi Muffler. Yamano, who is involved in art direction and graphic design in various fields and has a long-standing relationship with Yamatomichi founder Natsume. They share behind-the-scenes story of how they came up with these upcycled products together.
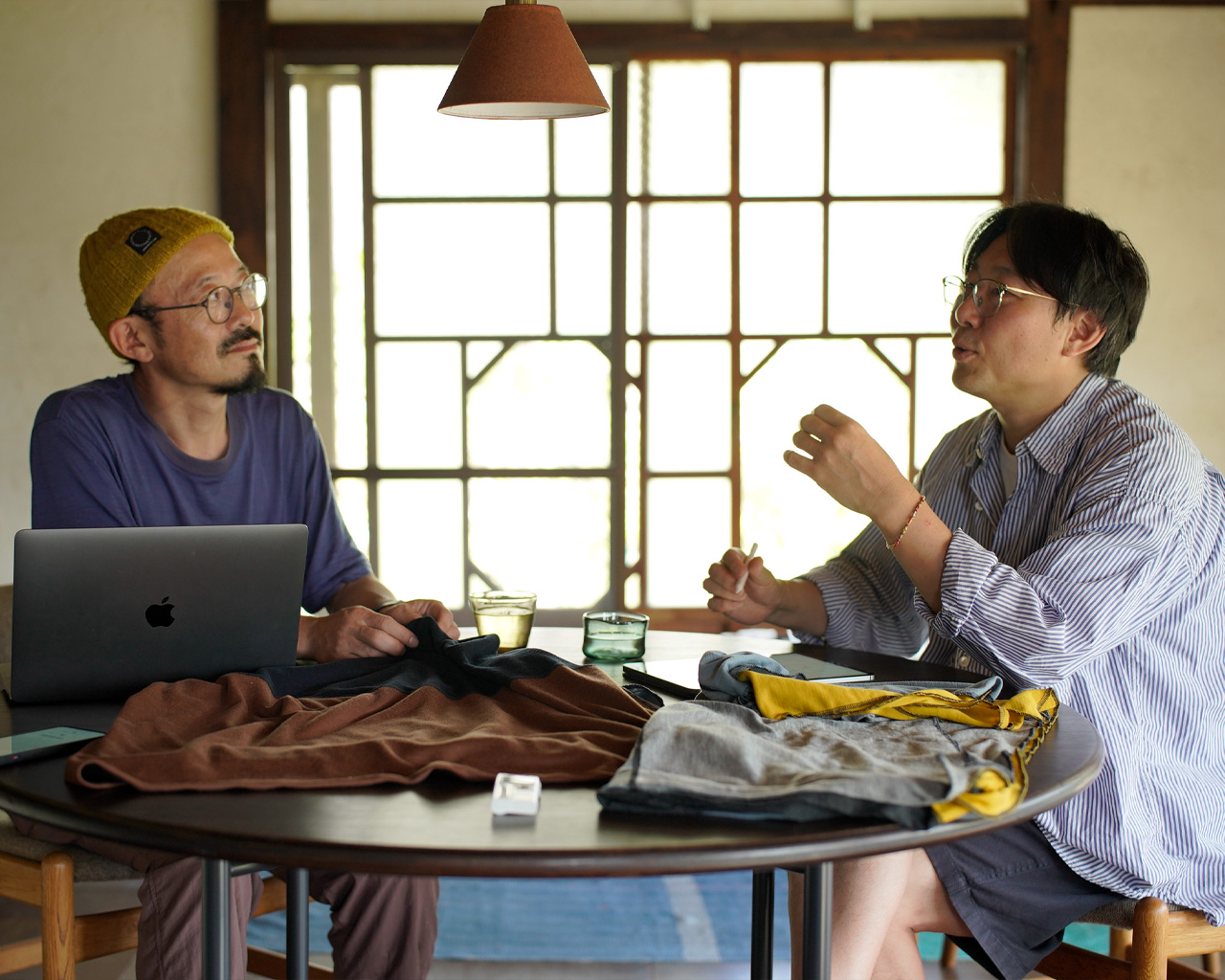
Akira We ended up with quite a surplus of fabric used in the cuffs and such during the production for the 100% Merino Pullover and 100% Merino Hoody. We couldn’t regular products with it, and I was really troubled about what to do. We discussed what to do with the entire company for a long time, and in the midst of that, we came up with the idea of making something other than hiking gear.
However, we are a gear manufacturer, and if we simply made blankets or scarves, they probably wouldn’t sell well, and people might wonder why we’re making such things. So, because we want to make something that we believe in and want, we decided to ask someone who was very talented to design it. And the person who came to mind was Mr. Yamano.
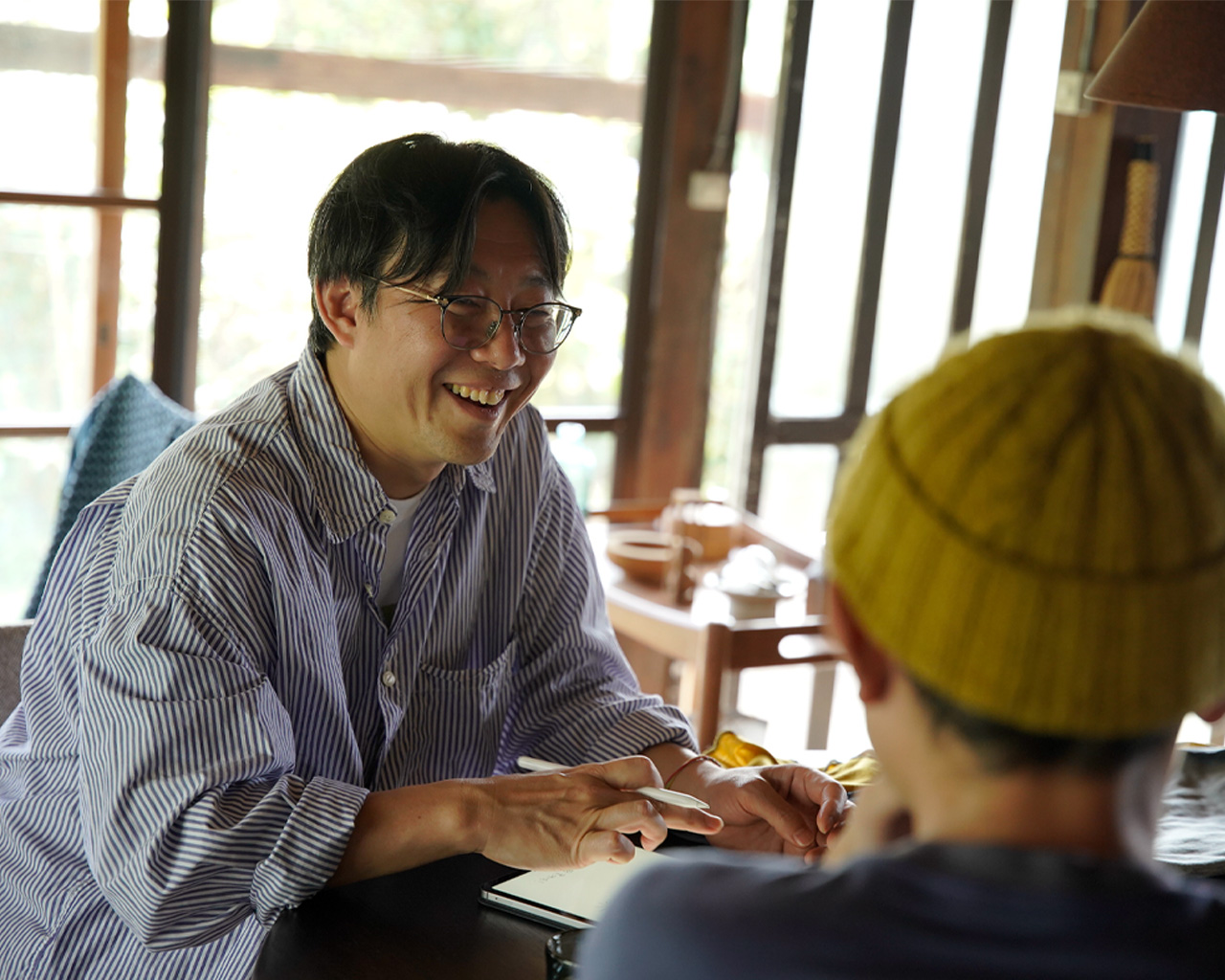
Hideyuki Why you reached out to me, even though I am not in the business of making products.
Akira I’ve known you for about 20 years, so first of all, I know your personality well. And for this project, it wasn’t just about creating superficially beautiful designs; we needed to think about how to use the fabric, how to incorporate it into the products with limited material, and we needed to think through the process carefully to design it properly. I believed that with you, we could bring you our problems, and come through with a solution together, and see it through to the end.
Hideyuki My usual work involves discussing and creating from a structural perspective rather than just designing something decoratively. This time, it wasn’t just about thinking of patterns; we discussed conditions like how many meters of fabric were left and what types of fabric were available. The initial meeting, went very well.
Akira When we had the first meeting at Daibutsu Laboratory, the design was almost finalized!
Hideyuki Yes, indeed it was. Usually, in graphic design, there’s a theme but with conditions, and we solve them. But this time, I could relate to the project’s origin, so it was a more smoother process. It was rewarding to work on a product that conveyed your philosophy.
Initially, we got a list showing how many meters of each color fabric were available. I intuitively understood that we needed to start by understanding this. Regarding the design, we considered the size of the blanket and decided on five parts to allocate the fabric. As I sketched it out, I saw mountains at the top and a path at the bottom, creating a road. The idea of Yamatomichi “mountains and path” emerged naturally.
The fabric itself stretches quite a bit, which adds to its comfort, but we were also concerned about excessive stretching. By designing it as a pattern, the sewing process helped control the stretch. The thematic graphic of “mountains and paths” aligned well with the functionality it brought.
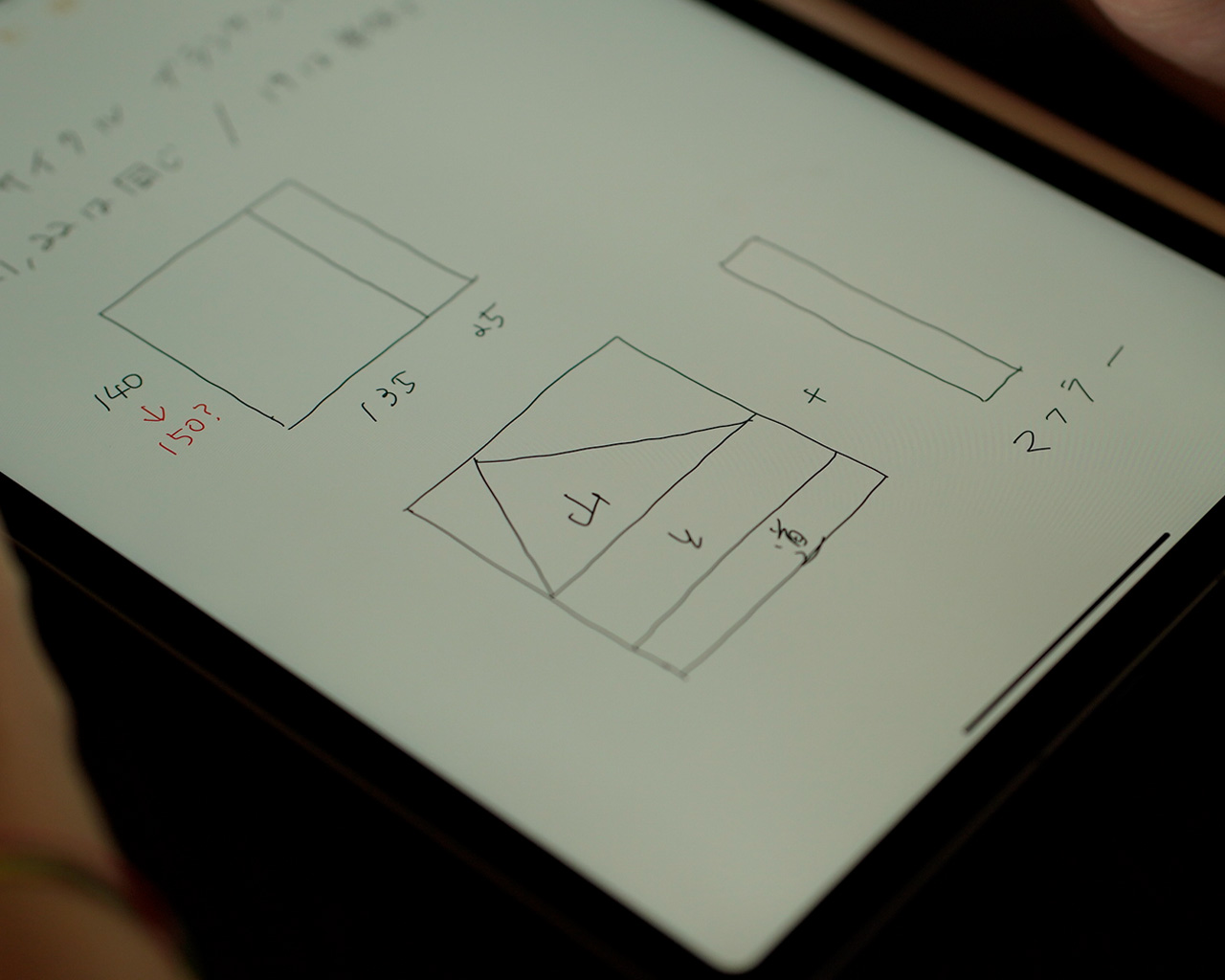
Akira What was particularly challenging for you?
Hideyuki I think the most challenging part was breaking down the surplus fabric lengths into usable pieces, kind of like solving a puzzle for the five parts. We had to figure out how many pieces we could get from each fabric and then list the color combinations.
Akira That sounds like a headache! (laughs)
Hideyuki It felt more like solving a puzzle than designing, to be honest! (laughs).
Akira How did you feel when you saw the finished product?
hideyuki During the first sample, having two layers of fabric made it slightly stiff and heavy, right? We initially thought of using two layers for the sewing process, but we found out that we could sew it flat with just one layer. When we tried it with one layer, it became lighter, fit the body better, and the fabric felt nice against the skin. It draped well and felt comfortable to wear, which was great.
Regarding the design, we ended up with nine variations based on the surplus fabric distribution. As a result, we achieved a wide range of designs, from vibrant ones with yellow and blue to more subdued ones with gray. This variety adds to the visual appeal, and it’s heartwarming to see.
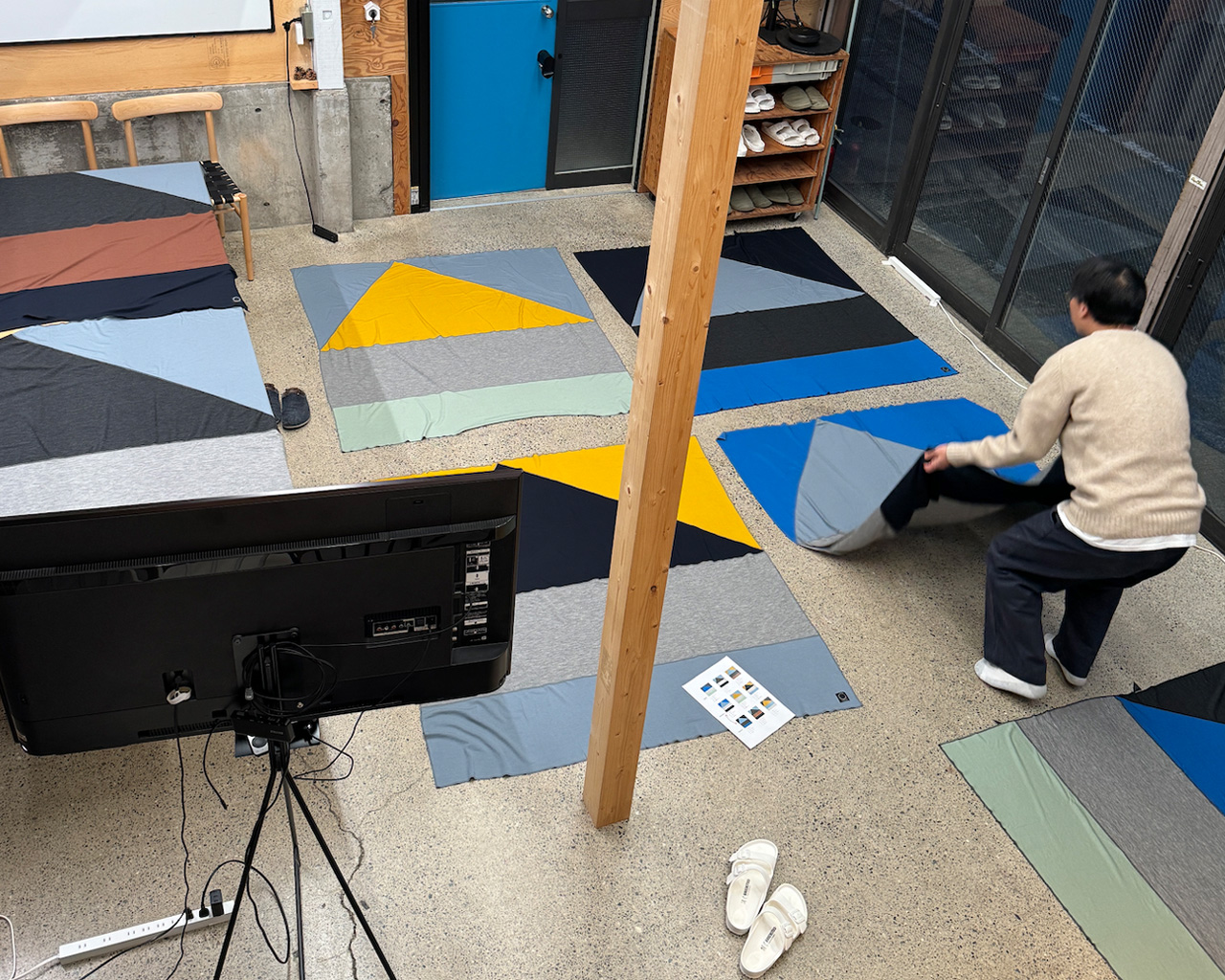
Akira It has a great presence, doesn’t it? Just spreading it out makes you happy. We’ve had prototypes made and used them for about 1-2 months. What are your thoughts?
Hideyuki I’m based in both Tokyo and Naha, so there’s a temperature difference. Sometimes I wear it over my shoulders while working. In Okinawa, people often wear shorts, but when it gets a little cooler, I wrap it around my waist or use it as a knee blanket. Also, it feels nice to lightly drape it over when I want to lie down for a bit.
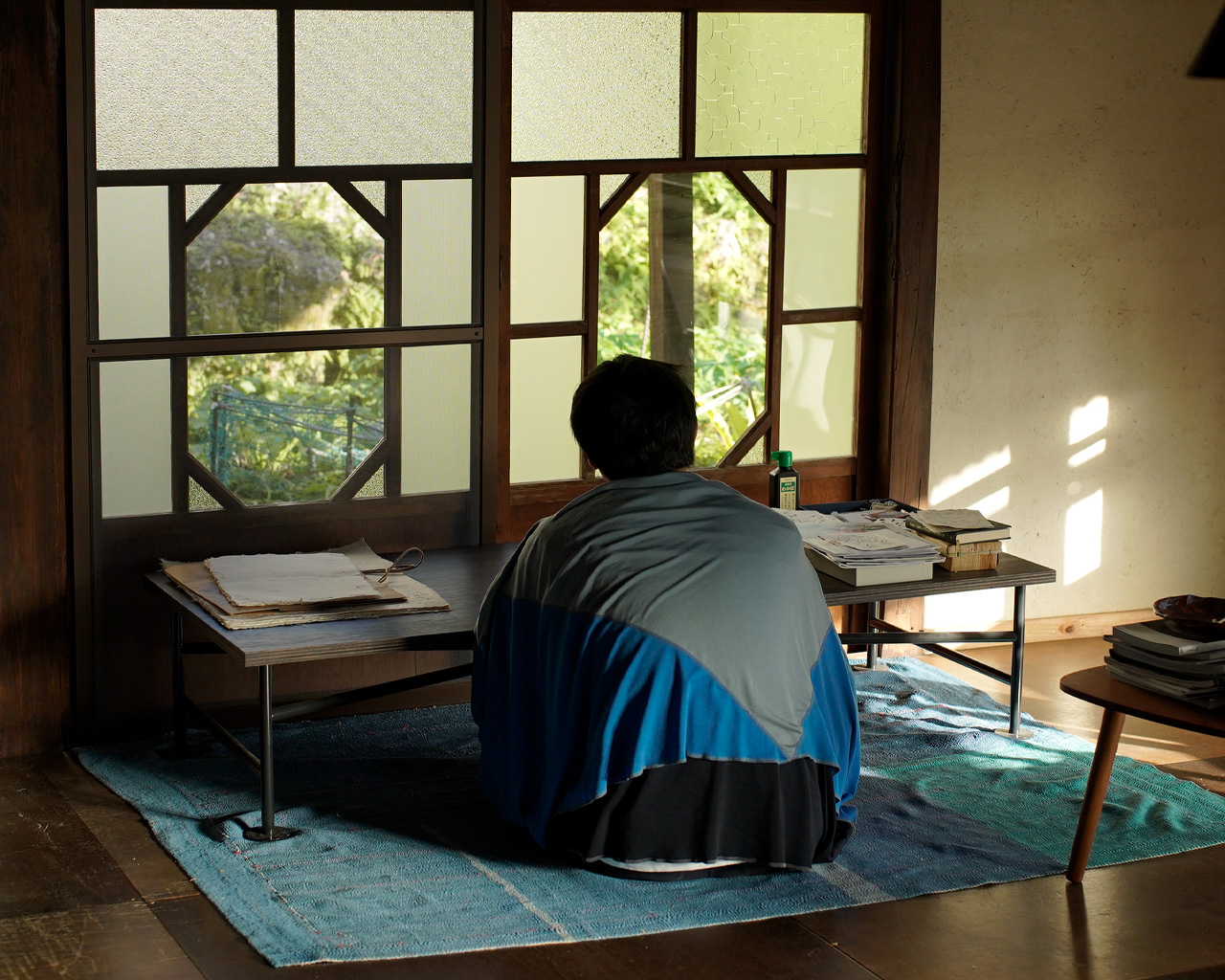
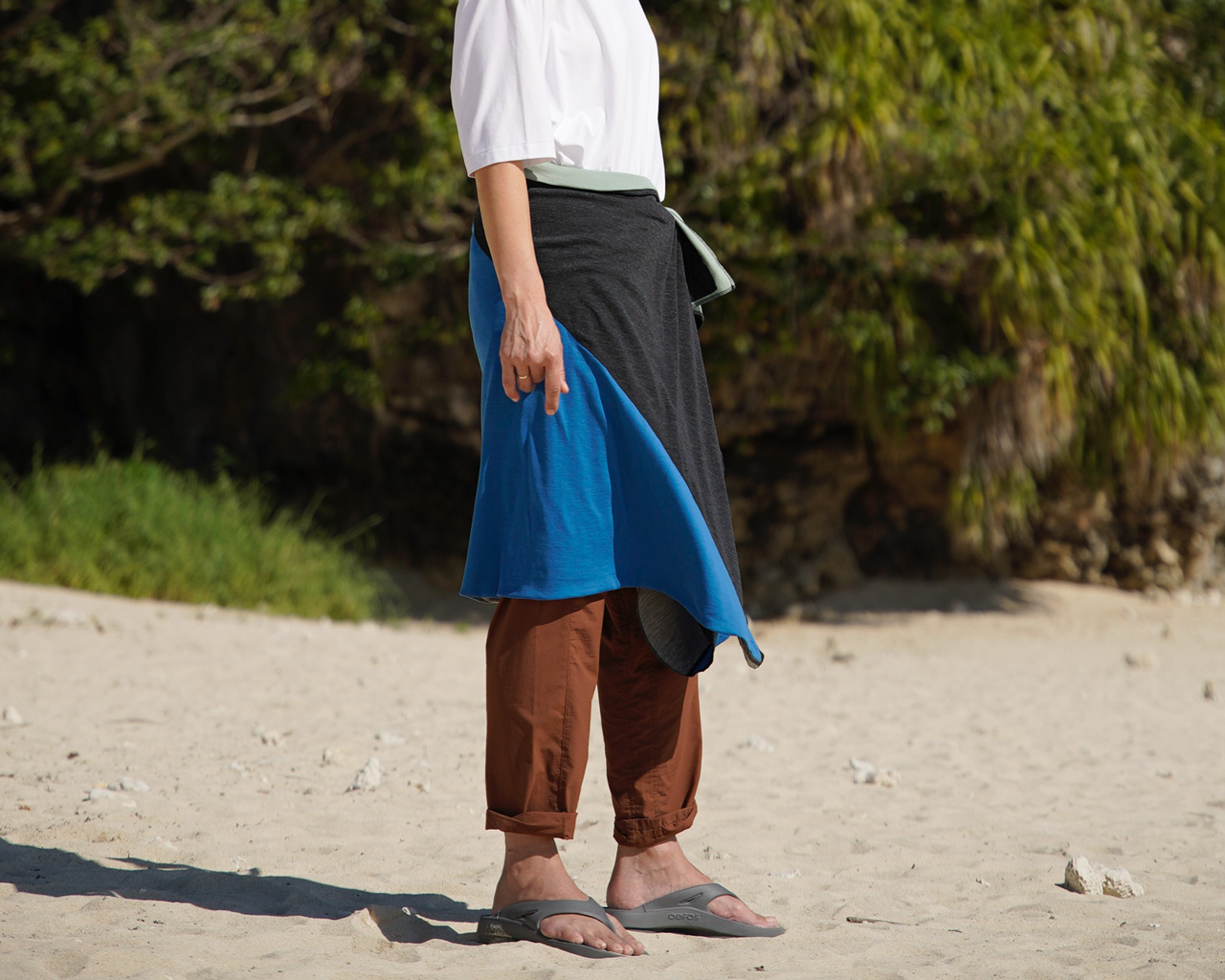
Akira The reason behind the creation of the scarf was also interesting, wasn’t it?
Hideyuki Yes, it was also a coincidence. When we first verified the size of the blanket, the width we decided on was slightly narrower than the standard fabric width. So, we ended up having some leftover strips, which happened to be suitable for a scarf in terms of length. Since a scarf benefits from being double-layered for thickness, it was eventually created as a design combining colors on both sides.
Akira In any case, we used up everything! (laughs) The texture of the merino wool is really nice, so when you wear it or wrap it around, it feels incredibly comfortable. I really hope people give it a try.
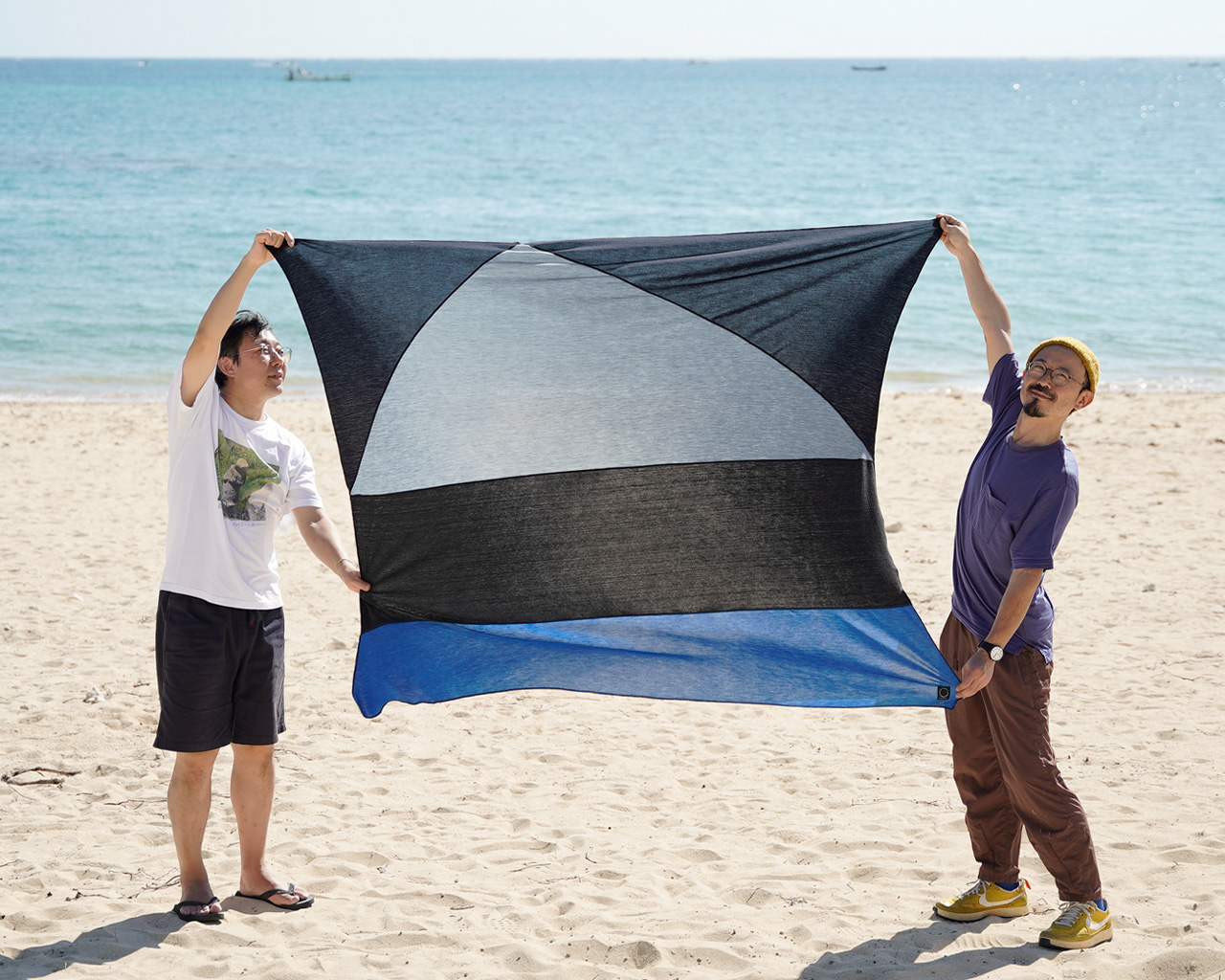
On February 2, 2024, in Naha.
Form and Function
Zero-waste
The design was utilized to prevent wasting surplus Merino wool. The scarf was born from the remaining fabric that was leftover from creating the Yamatomichi Blanket.
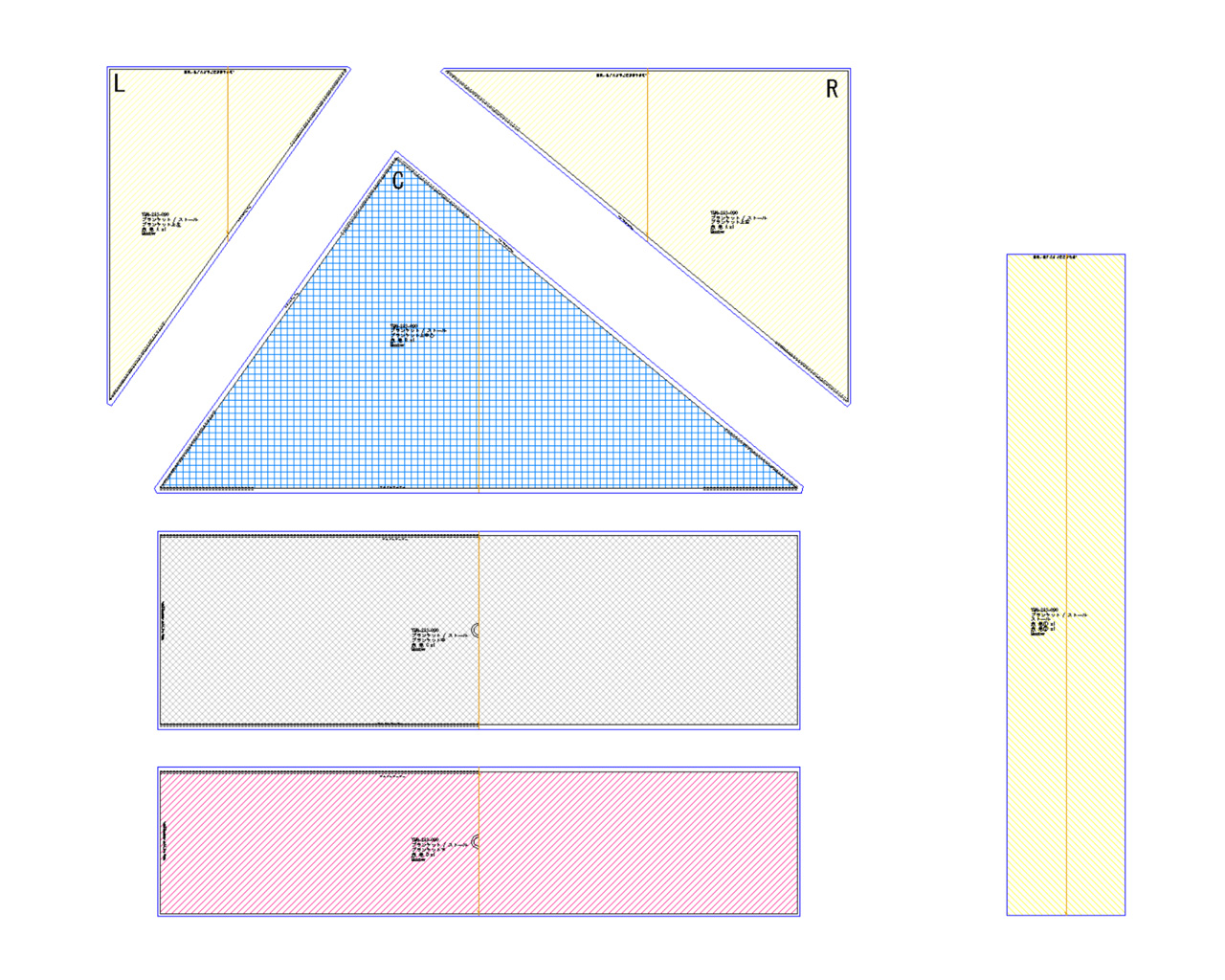
Details
Although its quick-drying properties may not match those of synthetic base layers, it prioritizes moisture absorption and warmth over quick-drying and cooling. Merino wool reduces the risk of body temperature dropping due to wetness from rain or sweat, as it keeps warm even when wet.
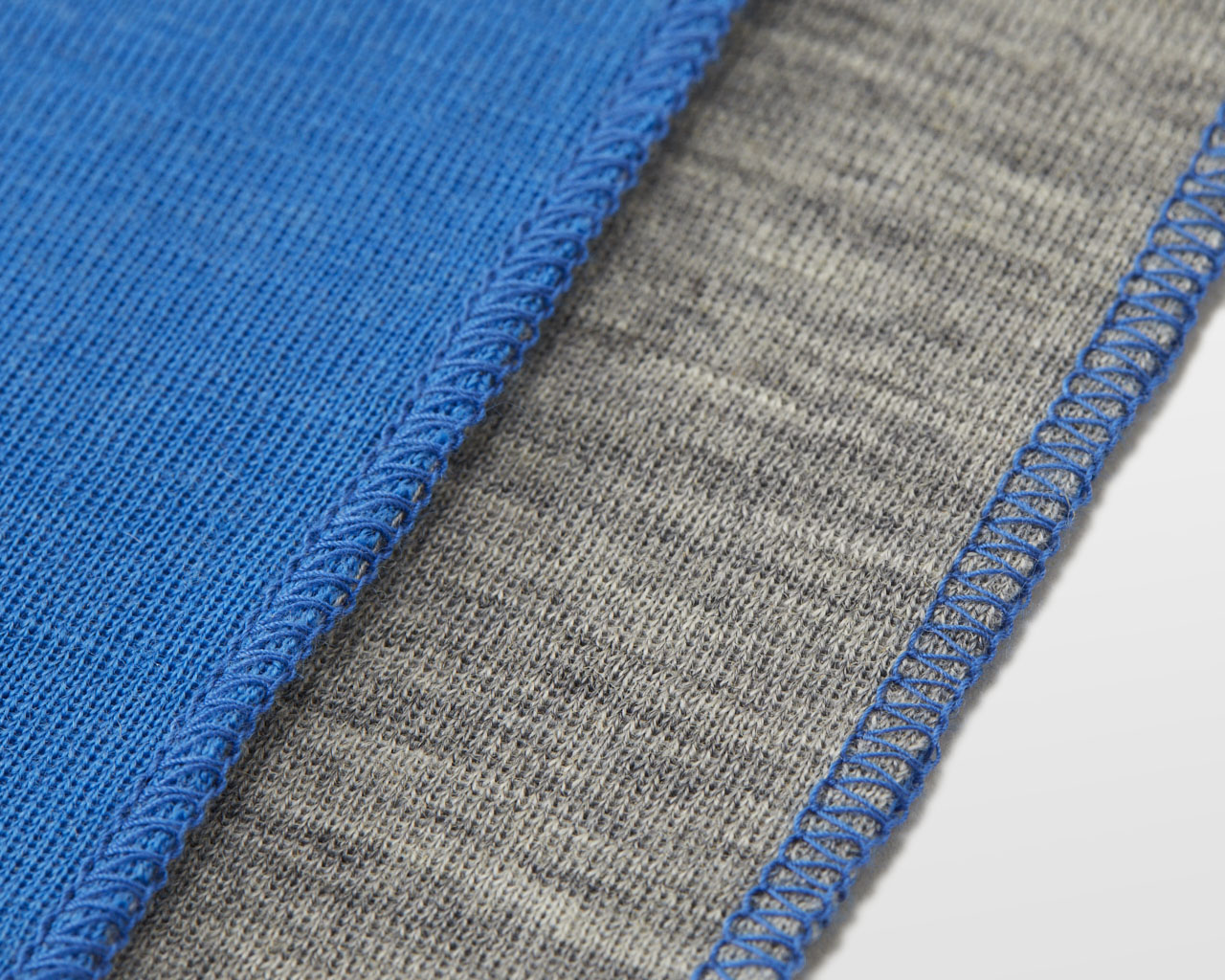
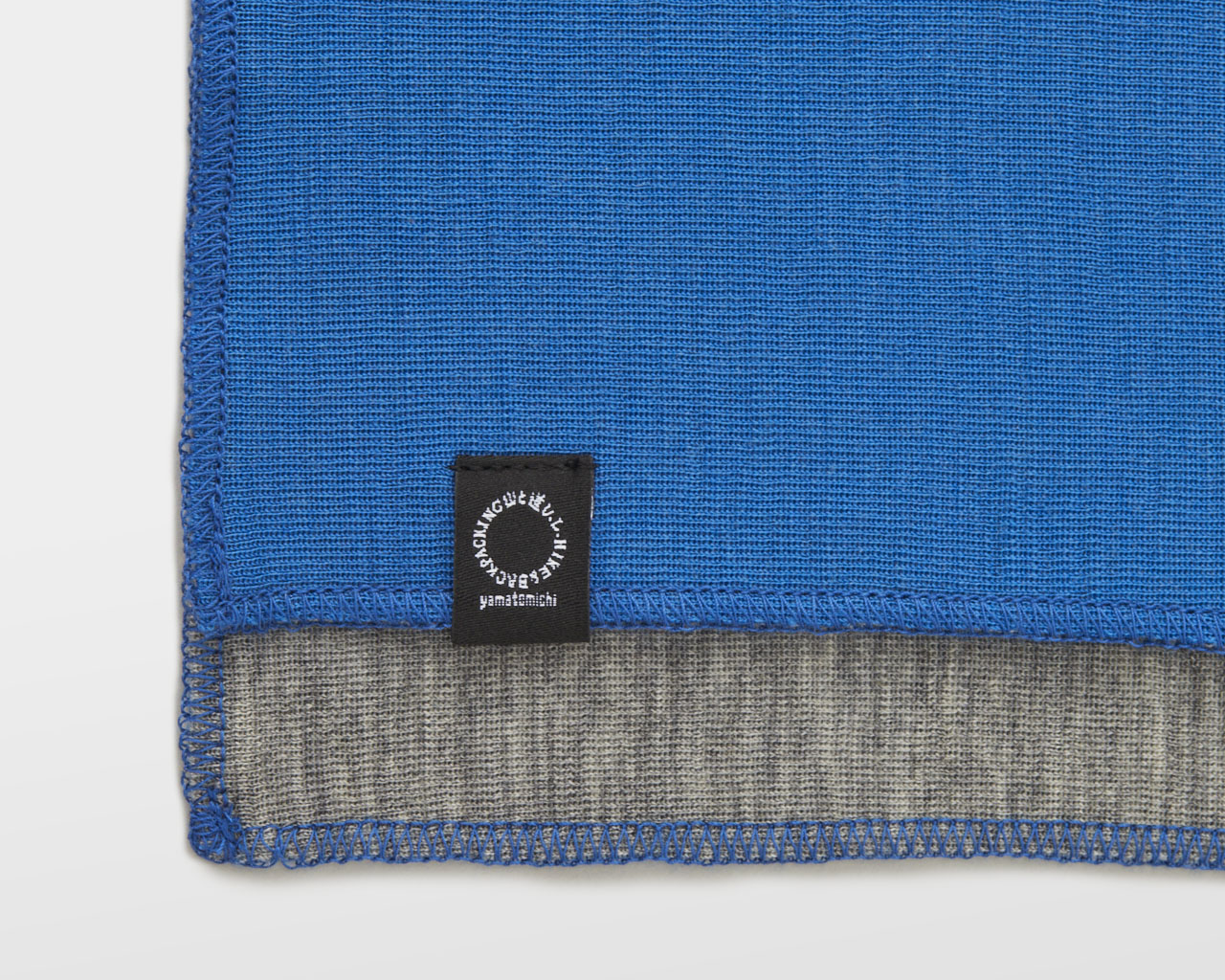
Material
Zero-waste
We used ribbed sections for the neck and cuffs of the 100% Merino wool line-up. The material is a type of knit fabric that stretches horizontally, and it has high elasticity and resilience. Manufactured in Omi, a woolen fabric production area in Japan, provides a comfortable feel against the skin. Since the material was for cuffs, it is slightly thicker, which enhances its insulation properties, yet it remains highly breathable, minimizing humidity build-up.
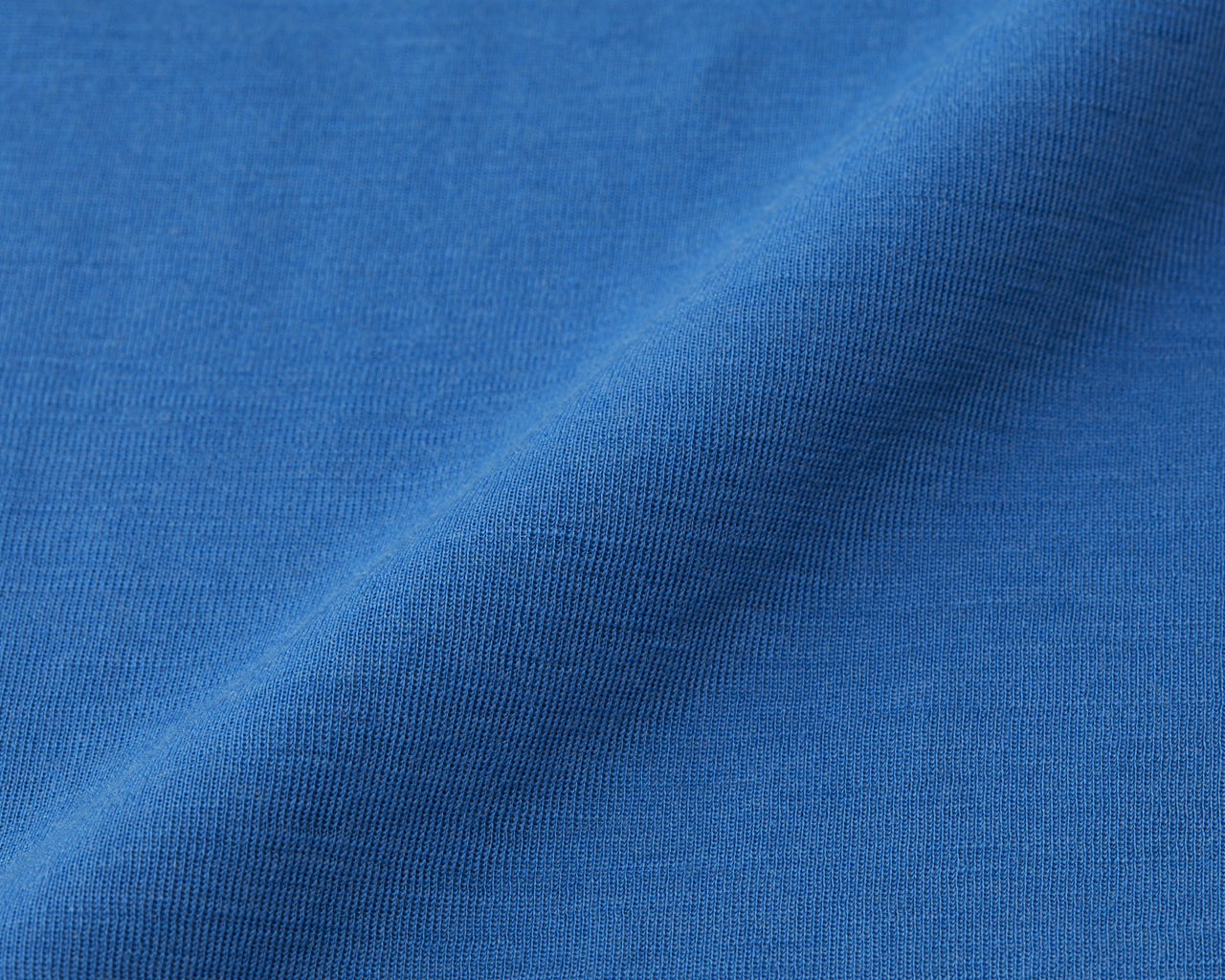
100% Merino Wool
Fabric Weight: 230-240g/m²
Yarn Count: 1/52
Tensile Strength (JIS L1096A): 290kPa
(Pressure value when the fabric tears with a rubber membrane applied to it)
Insulation (JIS L1096A): 34.3%
(Energy loss of the heat source when the fabric is placed on it)
Care Instructions
Instructions
Merino wool, being a natural fiber, possesses excellent temperature and moisture regulation as well as odor-resistance properties. However, it also has weaknesses such as susceptibility to insect damage and abrasion, which can lead to yarn breakage and easily create holes.
For inquiries regarding repairs due to holes or deterioration over time, such as patching or mending, please feel free to contact us through the SUPPORT page at “Repair Inquiries”.
Repairing with Felting:
Holes caused by yarn breakage or insect damage can be repaired through a technique called felting, where wool fibers are interlocked using special felting needles. At Yamatomichi, we also offer repairs using felting with wool fibers in the same color as the product.
For more information on the felting repair method and repairing Yamatomichi Merino wool knitwear products, please refer to our JOURNALS article “Repairing Holes in Merino Wool: A Guide from Yamatomichi Repair Department #1”.
Care Instruction Page
For more detailed washing, drying and water repellent care instructions, visit our SUPPORT Page. With proper care you can prolong the funtionality of the product.
Repair
Merino wool, being a natural fiber, possesses excellent temperature and moisture regulation as well as odor-resistance properties. However, it also has weaknesses such as susceptibility to insect damage and abrasion, which can lead to yarn breakage and easily create holes.
For inquiries regarding repairs due to holes or deterioration over time, such as patching or mending, please feel free to contact us through the SUPPORT page at “Repair Inquiries”.
Repairing with Felting:
Holes caused by yarn breakage or insect damage can be repaired through a technique called felting, where wool fibers are interlocked using special felting needles. At Yamatomichi, we also offer repairs using felting with wool fibers in the same color as the product.
For more information on the felting repair method and repairing Yamatomichi Merino wool knitwear products, please refer to our JOURNALS article “Repairing Holes in Merino Wool: A Guide from Yamatomichi Repair Department #1”.